Dampfverdichtung auf höchstem Niveau
Hochdruck- und Hochtemperaturverdichter für Brüden- und Dampfanwendungen
Eine Kombination aus leistungsstarker Verdichter- und Kompressortechnik: mit dem VapoMaxX, einem Produkt unserer VapoLine.
Vorteile unseres VapoMaxX für die Mechanische Brüdenverdichtung und Dampfregenerationsverfahren
Das Design des VapoMaxX ist eine Kombination aus den Vorteilen unserer überlegenen Verdichter und der fortschrittlichen Leistung der Kompressortechnologie.
Unser Design ermöglicht sehr flexible Installationen und Anordnungsmöglichkeiten von einstufigen und in Reihe geschalteten Maschinen, auch auf bei höheren Installationsniveaus.
Zur Maximierung des Verdichtungsverhältnisses und zum Erreichen maximaler Temperaturerhöhungen kann unser VapoMaxX auch in Reihenschaltung installiert werden.
Der VapoMaxX auf einen Blick: |
---|
|
Energieeinsparungen und Verringerung der CO2-Emissionen in der Prozessindustrie
Neudefinition des Niveaus der Abwärmenutzung in der Prozessindustrie
Mit dem VapoMaxX wird die thermische Energie der bisher ungenutzten Abwärme, die am Ende eines Produktionsprozesses frei wird, genutzt, um letztlich Dampf mit höherem Druck und deutlich höherer Temperatur für Prozesse bereitzustellen.
PILLER bietet eine Lösung für diese Prozessbedingungen in Bezug auf Temperatur- und Druckanstieg und passt das Systemdesign an die Anforderungen der Produktionsanlagen an.
Unser VapoMaxX zeichnet sich durch seiner Verdichtertechnologie für Brownfield-Projekte, die Nachrüstung bestehender Anlagen sowie für den Einsatz in Neuanlagen mit maximaler Effizienz und Langlebigkeit aus. Dies führt zu Kosteneinsparungen und damit einhergehend zu niedrigen Lebenszykluskosten.
Wir bedienen verschiedene Projekte mit der Vapor Compression Heat Pump Technology von PILLER, die unsere Antwort auf die steigenden Energiekosten ist.
Die Ergebnisse eines unserer Projekte: Durch die Implementierung eines achtstufigen VapoMaxX-Systems erzielt unser Kunde signifikante Energieeinsparungen von rund acht Millionen Euro pro Jahr und eine erhebliche CO2-Reduktion von 10.650 Tonnen pro Jahr.
Erfahren Sie mehr über industrielle Wärmepumpen von PILLER
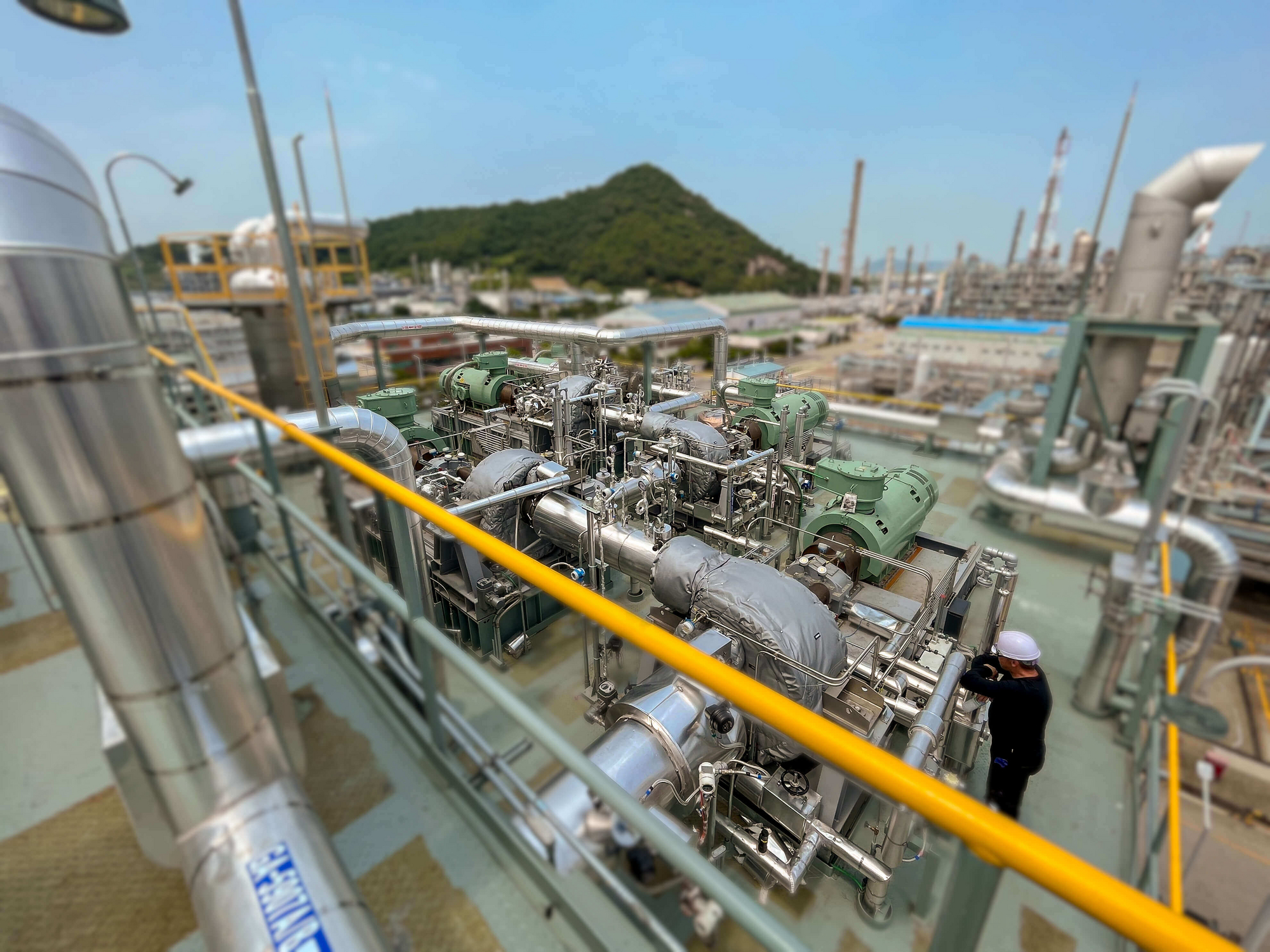
Die wichtigsten Merkmale des PILLER VapoMaxX
Leistungsübersicht über unsere VapoMaxX-Produktpalette
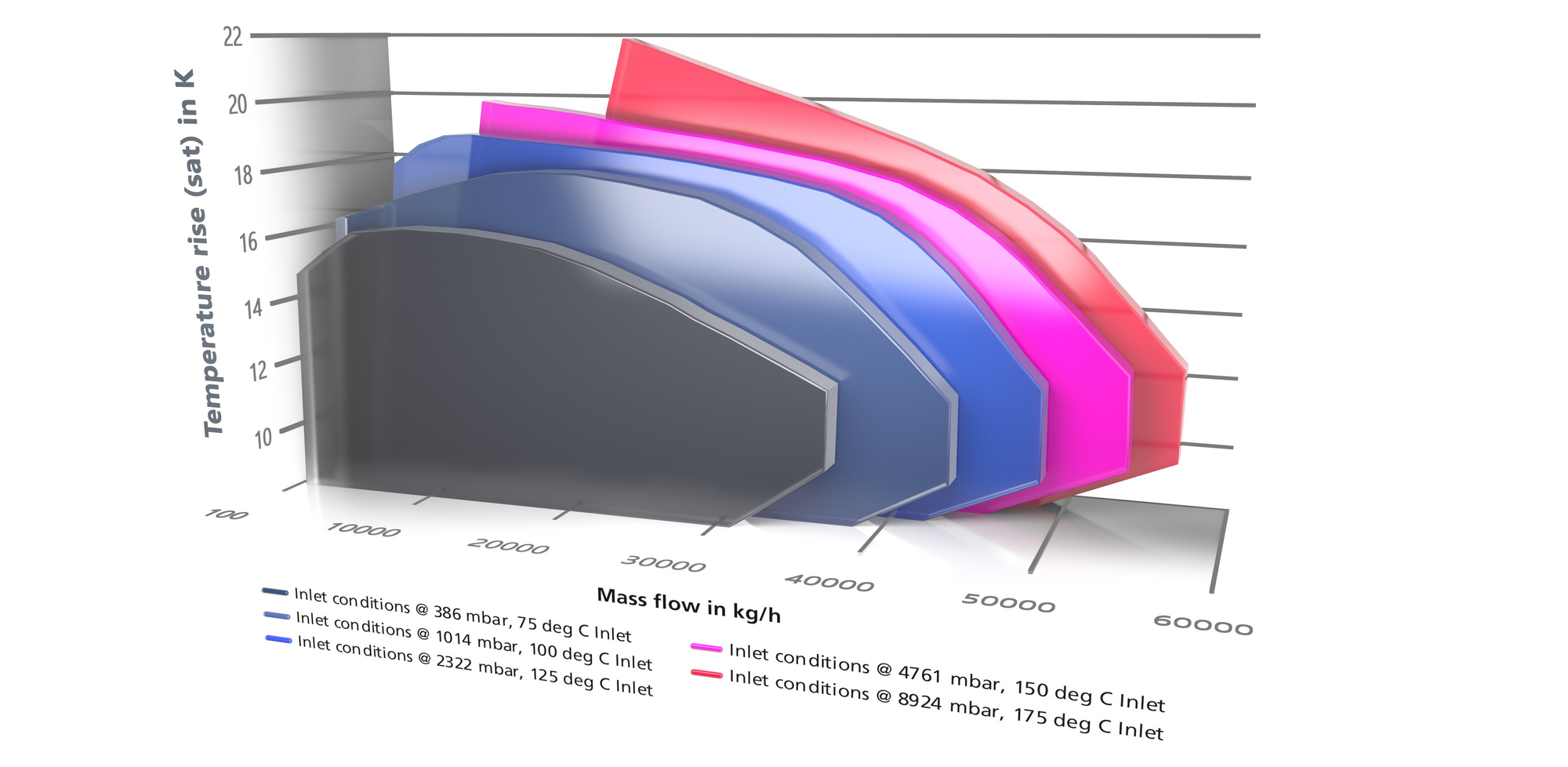

Die ideale Lösung für effiziente Prozessabläufe
Einfache Installation, kurze Ausfallzeiten und geringerer Wartungsaufwand
Die Konstruktion des PILLER VapoMaxX gewährleistet eine ideale Lösung für verschiedene Prozesse und Anwendungen in der Prozessindustrie.
Unsere Konstruktion ermöglicht eine einfache Installation in Stahlkonstruktionen unterschiedlicher Höhe, so dass kein spezieller Zugang oder spezielle Ausrüstung erforderlich ist.
Die einzigartige ausziehbare Rotoreinheit der Maschine sorgt für kürzeste Stillstandszeiten in Ihrer Produktion, da die Hauptrohre an Ort und Stelle bleiben können.
Im Vergleich zu Kompressoren vom internationalen Markt benötigt der VapoMaxX-Verdichter deutlich weniger Wartungsaufwand. Da nur wenige Komponenten wie Dichtungsringe, Lager, Filter und Öl gewartet werden müssen, können Sie den VapoMaxX schnell und einfach wieder in Betrieb nehmen.
Außerdem ist der Zugang zum Laufrad in kürzester Zeit möglich, so dass weder zusätzliche Kräne noch große Teams für Wartung und Service benötigt werden.
MVR/MVC -Verdichtertechnik
Kombination der Vorteile von Verdichtern mit der fortschrittlichen Leistung von Kompressoren
Die besonderen Eigenschaften der Maschine machen den PILLER VapoMaxX zu einer idealen Lösung für ein breites Spektrum von Prozessen und Anwendungen.
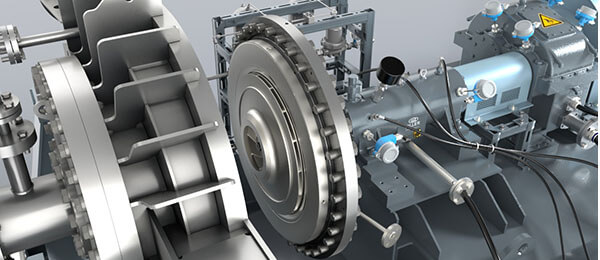
Ausziehbare Rotoreinheit
Für eine einfache Wartung und Instandhaltung hat PILLER eine ausziehbare Rotoreinheit entwickelt: PILLER hat einen beweglichen Sockel konstruiert, der alle rotierenden Komponenten enthält - mit mechanischer Drehvorrichtung. Die Rohrleitungen können für kürzeste Stillstandszeiten in Position bleiben.
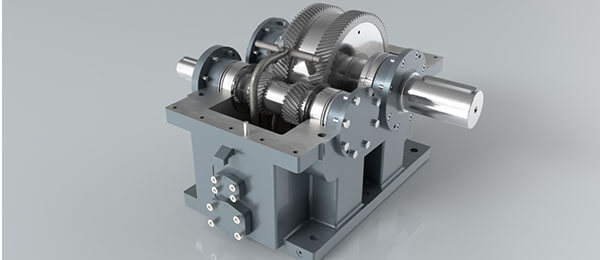
Getriebe
Das Getriebe wurde als Doppelschrägverzahnung entwickelt, was zu einer reibungslosen Kraftübertragung und erheblich reduzierten Geräuschemissionen führt. Ausgestattet mit Instrumenten zur Überwachung von Lagertemperatur, Vibration und Öldurchfluss lässt es sich in jede Sicherheitsüberwachung einbinden.
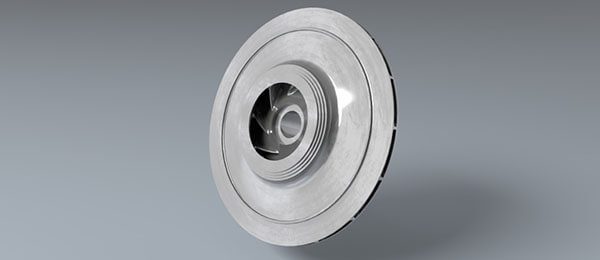
Optimierte Laufradausführung
Das Design unserer Laufräder wird ständig optimiert. Neue Leistungsanforderungen erforderten ein spezielles Laufraddesign für alle VapoMaxX-Typen. Für diese Entwicklung wurden zusätzlich neue Fertigungsverfahren getestet und etabliert.
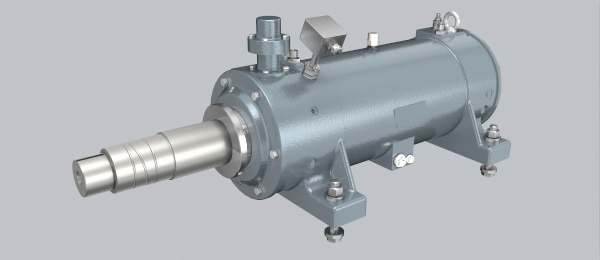
Quetsch-Öl-Dämpfer
Um die Lager so zu versteifen, dass der Spielraum zur kritischen Drehzahl groß genug für einen sicheren Betrieb ist, oder um die Steifigkeit für einen überkritischen Betrieb abzuschwächen, hat PILLER eine Standardlösung entwickelt: den Quetsch-Öl-Dämpfer.
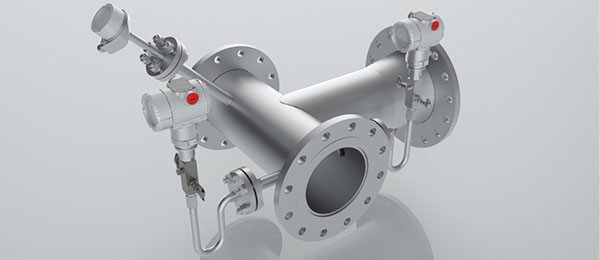
Überspannungskontrolle & -schutz
Für einen reibungslosen, sicheren und zuverlässigen Betrieb sind eine Überspannungskontrolle und ein adaptives Schutzsystem installiert. Diese Systeme lösen das Öffnen von Regelventilen automatisch aus – um den Mindestdurchfluss aufrechtzuerhalten oder um aufeinanderfolgende Druckstöße zu vermeiden.
MEHR INFORMATIONEN ÜBER DEN PILLER VAPOMaxX
Weitere detaillierte Informationen finden Sie in unserem Produktblatt zum PILLER VapoMaxX:

Weitere PILLER Produkte
Kontakt
Piller Blowers & Compressors GmbH
Nienhagener Str. 6
37186 Moringen
Deutschland +49 5554 201-0
+49 5554 201-271