Vapor compression at a new level
High pressure and high temperature compressor for vapor and steam applications
A combination of high-performance blower and compressor technology: with the VapoMaxX, a product of our VapoLine.
Advantages of our VapoMaxX for Mechanical Vapor Recompression and steam regeneration processes
The design of the VapoMaxX is a combination of the advantages of our superior blowers and the advanced performance of compressor technology.
Our design allows very flexible installations and arrangement options of single-stage and serial connected machines even at higher installation levels.
To maximize compression ratios and to reach maximum temperature lifts our VapoMaxX can also be installed in serial connection.
Our VapoMaxX at a glance: |
---|
|
Energy savings and reduction of CO2 emissions in the process industry
Redefining the level of reusing waste heat in the process industry
With the VapoMaxX, thermal energy from the previously unused waste heat released at the end of a production process is used to ultimately provide steam with a higher pressure and a significantly higher temperature for processes.
PILLER offers a solution for those process conditions in terms of temperature and pressure rises and adapt the system design for the requirement of production plants.
Our VapoMaxX stands out with its compressor technology for brownfield projects, the retrofitting of existing plants, as well for implementing in new installations with maximum efficiency and durability, resulting in cost savings and lower lifecycle costs.
We serve different projects with the Vapor Compression Heat Pump Technology made by PILLER, which is our response to rising energy costs.
The results of one of our projects: By implementing an eight-stage VapoMaxX system, our customer achieves significant energy savings of approximately eight million euros per year, resulting in a substantial CO2 reduction of 10,650 tons per year.
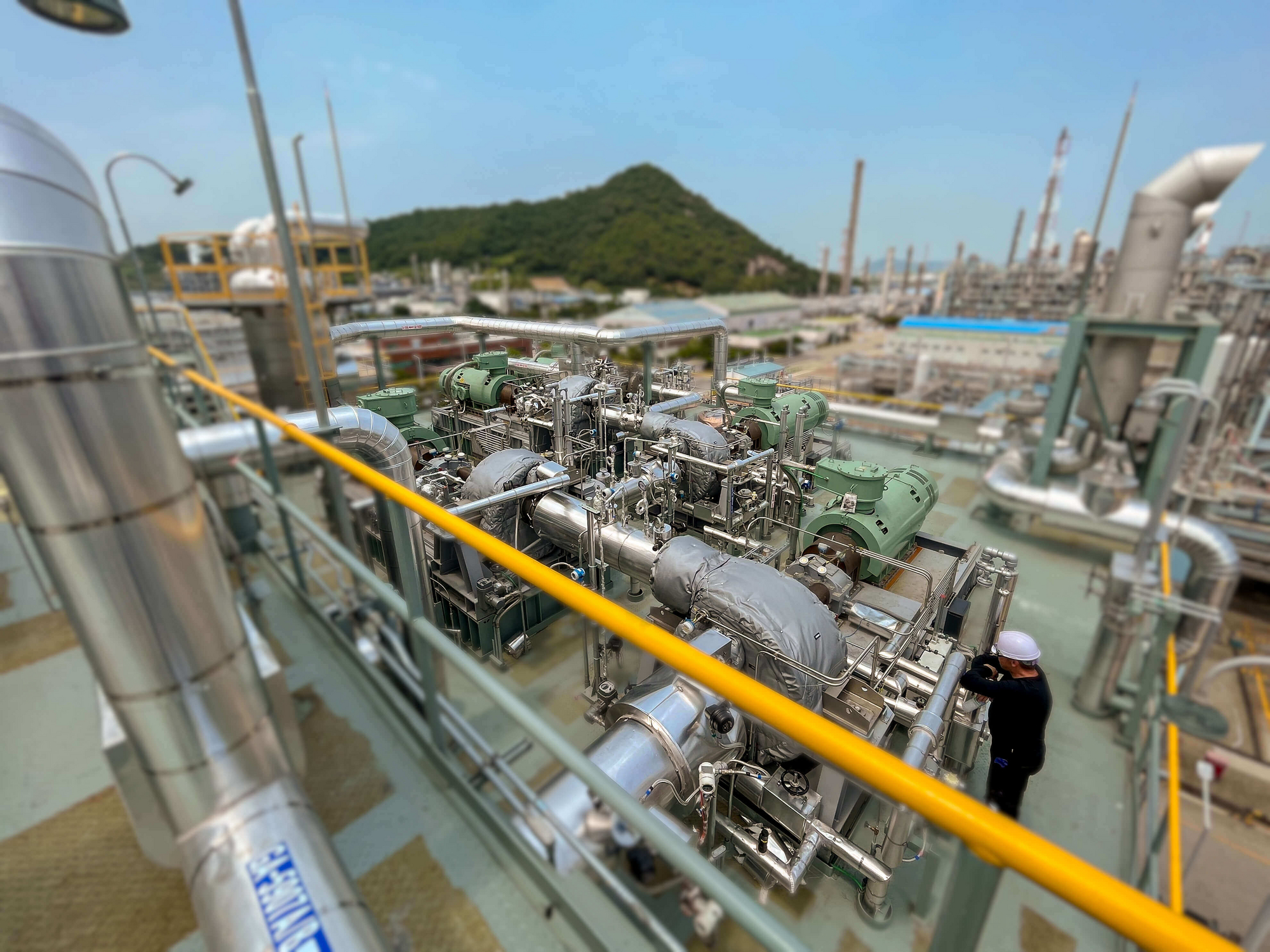
Key features of the PILLER VapoMaxX
Performance summary of our VapoMaxX product range
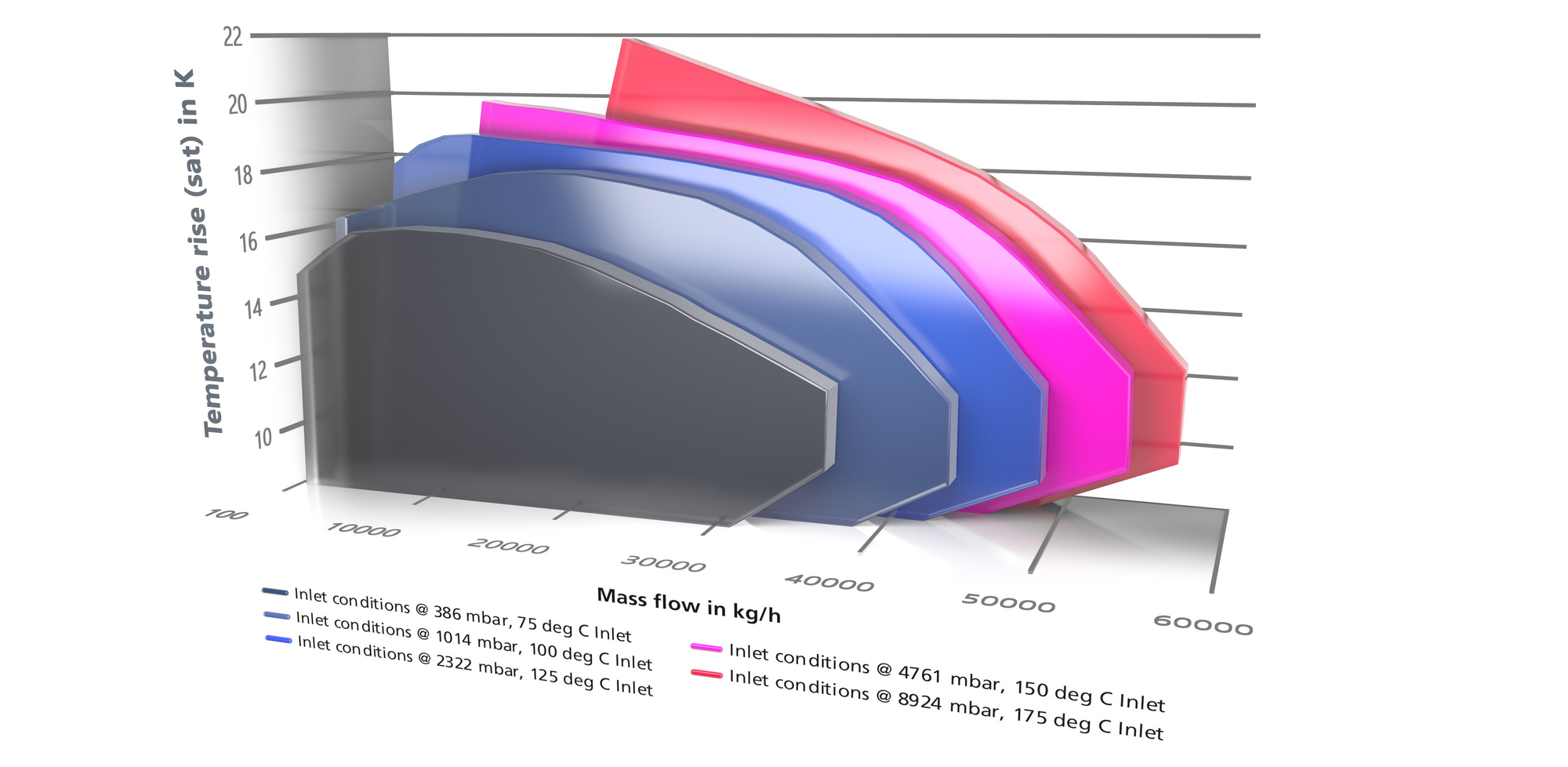
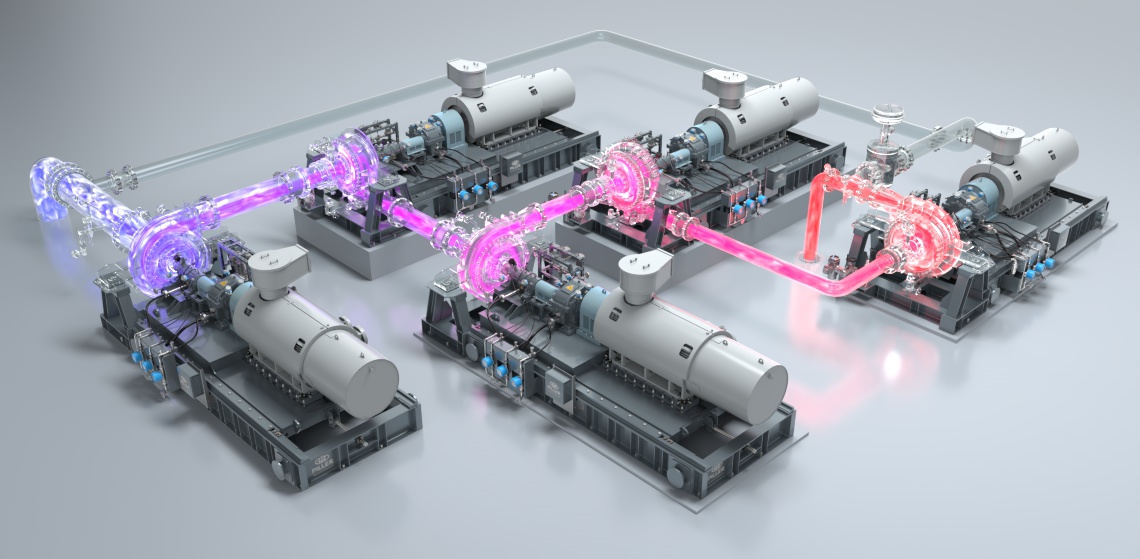
The ideal solution for efficient process operations
Easy installation, short downtime and reduced maintenance effort
The construction of the PILLER VapoMaxX ensures an ideal solution for various processes and applications in the process industry. Our design allows an easy installation in steel structures of varying heights, eliminating the need for specialized access or equipment.
The unique pull-out rotor unit of the machine provides shortest downtimes in your production because main pipes can stay in place.
In comparison to compressors from the international market, the VapoMaxX compressor requires significantly less maintenance effort. With only a few components needing attention, such as seal rings, bearings, filters, and oil, you can quickly and easily get the VapoMaxX back up and running.
In Addition, the access to the impeller is possible in the shortest possible time, so that neither additional cranes nor large teams are required for maintenance and service.
MVR / MVC compressor technology
Combining the advantages of blowers with advanced performance of compressors
The special features of the machine making the PILLER VapoMaxX an ideal solution for a wide range of processes and applications.
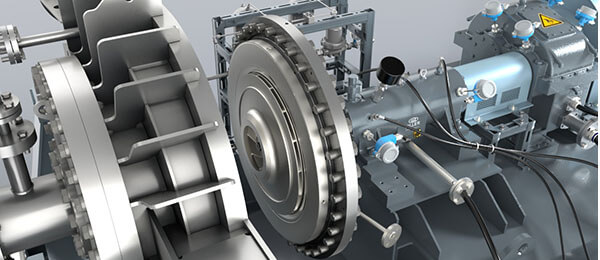
Pull-out rotor unit
For easy maintenance and service, PILLER installed a pull-out rotor unit: PILLER has designed a movable base which includes all rotating components – with mechanical crank. Vapor pipes can stay in place for shortest downtimes.
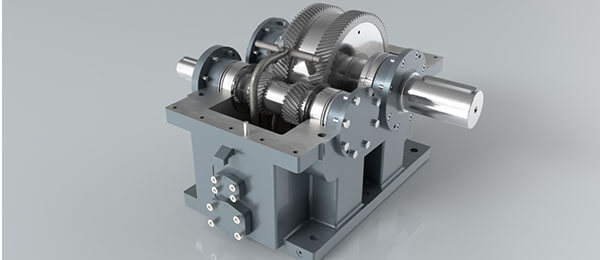
Gearbox
The gearbox is developed as a double helical gear design, leading to a smooth power transmission and significantly reduced noise emission. Equipped with instruments for monitoring of bearing temperature, vibration, and oil flow, it can be embedded into any safety monitoring.
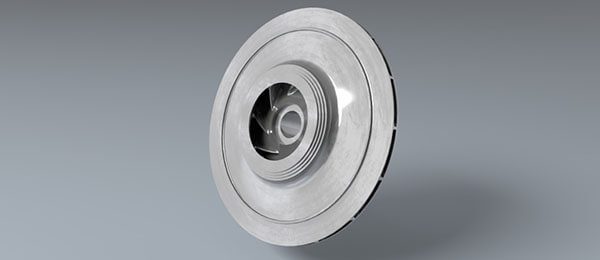
Optimized impeller design
The design of our impellers is constantly being optimized. New performance requirements demanded a special impeller design for all VapoMaxX types. For this development, new manufacturing processes were additionally tested and established.
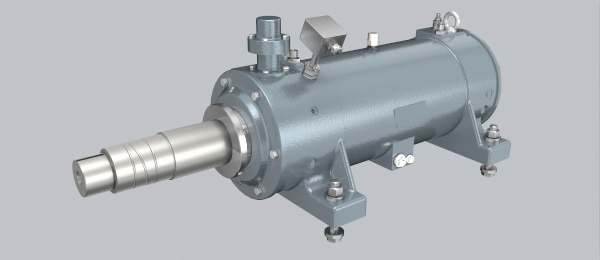
Squeeze Oil Damper Bearing
To either increase the stiffness of the bearings so that the safety margin to the critical speed is big enough for a safe operation or soften the stiffness for a supercritical operation, PILLER invented an off the shelf solution: the Squeeze Oil Damper.
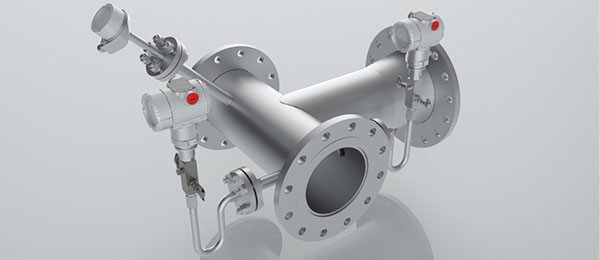
Surge Control & Protection
For smooth, safe, and reliable operation, a Surge Control and adaptive Surge Protection System are installed. This monitoring systems automatically trigger the opening of control valves - either to maintain the minimum flow rate or to prevent successive pump surges.
Learn more about PILLER
Contact
Piller Blowers & Compressors GmbH
Nienhagener Str. 6
37186 Moringen
Germany
+49 5554 201-0
+49 5554 201-271