Energy savings and reduction of CO2 emissions
Heat recovery with Vapor Compression Heat Pump Technology
PILLER leverages its expertise in Mechanical Vapor Recompression to apply its superior blower and compressor technology in industrial heat pump applications.
We develop the perfect solution for your process requirements to ensure that our blowers and compressor meet your specific needs. To find the ideal match for your process conditions, we will always engage you with full service from engineering over project management to design and manufacturing.
The range of applications for MVR blower and compressor solutions is constantly expanding through implementation of new technology. Presently, PILLER offers the capability to achieve a temperature increase (ΔT) of up to 20 K in a single-stage application.
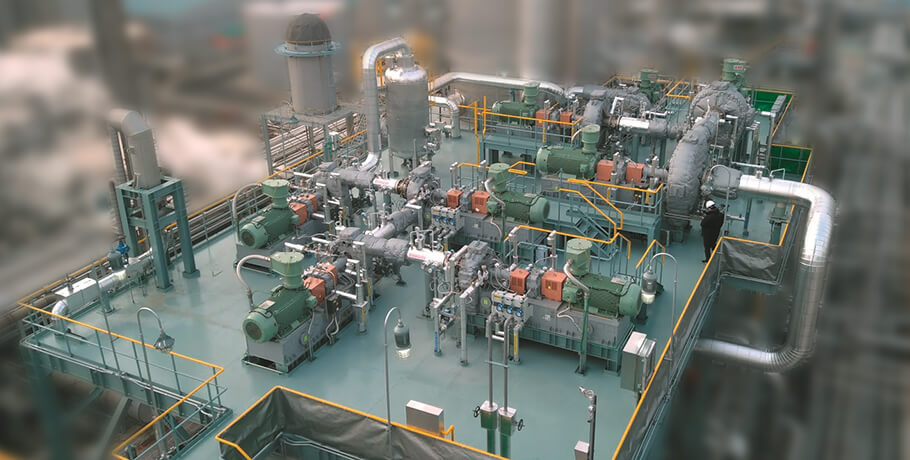
As a response to the rising energy costs and climate goals, generating or recovering steam using a heat pump is an attractive option.
The basic principle of the industrial heat pump solution made by PILLER is to recover waste heat and provide it at a usable temperature level for the process.
Key advantages: high primary energy savings, CO2 reduction and overall improved economic efficiency of the system.
The direct vapor compression cycle
The waste heat source is a vapor that can be compressed directly and then used for heating. The basic principle corresponds to the classic Mechanical Vapor Compression (MVR) process. In addition to being used for process heating, the compressed vapor can also be used in another process, or for generating steam or hot water.
The steam generation cycle
If the waste heat source is a liquid or a vapor that cannot be compressed, the heat pump cycle with evaporator can be used.
For this, water is used as a working fluid generating steam in the evaporator at a low pressure and temperature.
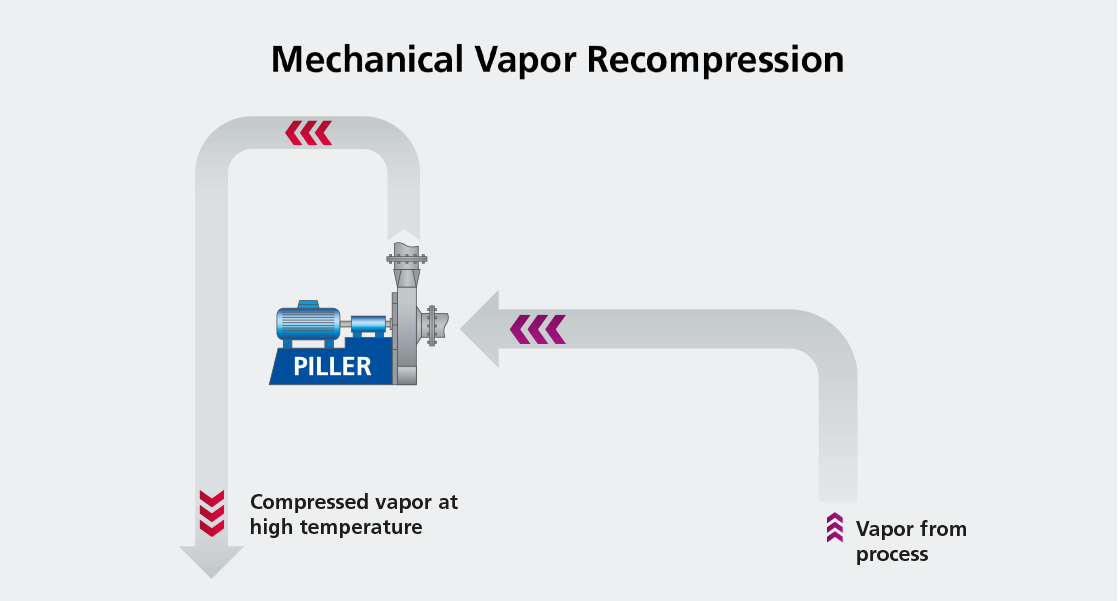
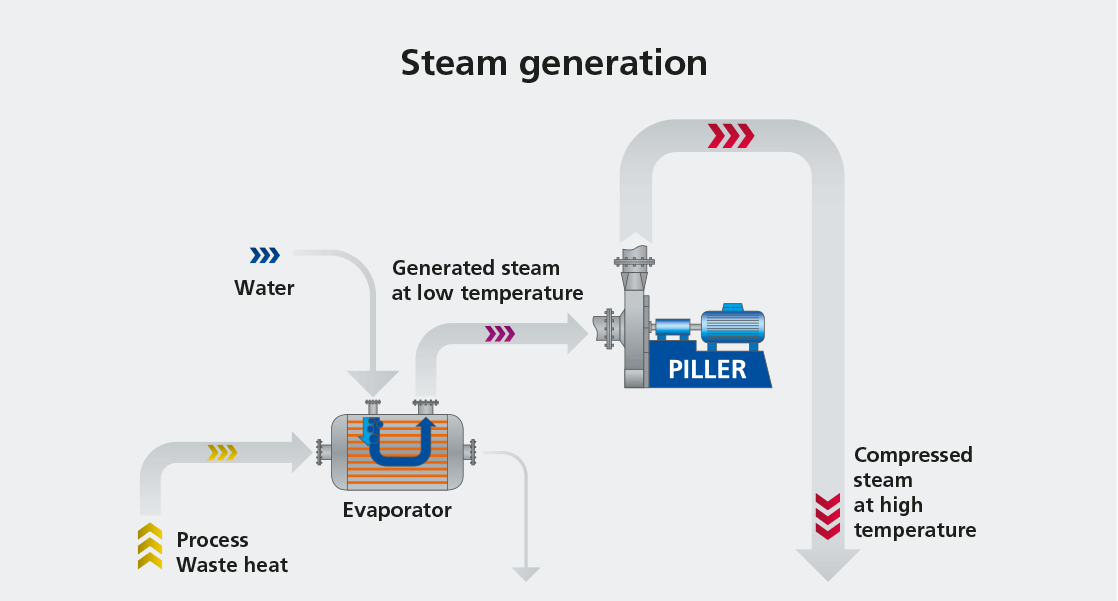
Maximizing energy efficiency and cost savings
Economic benefits of industrial heat pump systems
In energy intensive process industries with high steam demands, the system has proven itself in terms of economy and sustainability. Wherever thermal separation processes take place and there is a waste of heat, it is possible to retrofit – using our system.
The integration of a heat pump solution made by PILLER, and the resulting improved energy efficiency increases the cost-effectiveness of the plant by reducing energy costs with a short payback period.
The blowers and compressors technology can be used from vacuum – at a few millibars – up to a medium pressure level of 20 bar(g). On top of that PILLER stands for ease of maintenance and reliability, proven in decades of vapor (re-)compression on the market.
Environmental benefits of industrial heat pump systems
CO₂ emissions are reduced through the substitution of fossil fuels and, in contrast to conventional heat pumps, the heat pump solution made by PILLER does not use refrigerants which may be environmentally harmful, dangerous, or corrosive.
Our solution uses a commonly available fluid – process vapor or water – and thus contributes significantly to climate and resource protection.
The advantages are clear: higher energy efficiency due to the reuse of waste heat, reduced use of fossil fuels, lower CO₂ emissions and reduced energy costs – thanks to retrofitting your process.
Benefits of heat pump solution made by PILLER |
---|
Reductions in energy consumption and costs:
|
Improved climate protection and resource conservation thanks to reduced use of fossil fuels and more than 60% reduction in CO2 emissions |
Significantly improved energy efficiency through heat recovery |
Short payback period |
Simple integration into existing systems: retrofitting without great effort and easy implementation even in limited space conditions |
Applications in the process industry
Industrial Heat Pumps with vapor compression systems
Nowadays the process industry still releases large amounts of waste heat into the environment.
Our heat pump solution made by PILLER is ideal for those energy-intensive process industries with high steam demand. It can be used wherever thermal separation processes take place, like in manufacturing of products in the petrochemical, chemical, pharmaceutical, basic materials manufacturing, paper and food industries.
Whether distillation columns, desorption plants, concentrators, evaporative crystallizers or chemical reactions – once process steam or vapor is produced, the reengineering with this system is the best solution to achieve high coefficients of performance (COP) and a correspondingly high economic efficiency.
In the power range of several megawatts and for providing steam at a high temperature level, the heat pump solution made by PILLER is the solution for heat recovery in the process industry. COPs or seasonal performance factors (SEER) of 5 to 45 are possible, depending on the temperature rise, and ensure the quick amortization of the investment.
Transforming waste heat into usable energy
PILLER enables to recover surplus heat and to supply steam. Waste heat streams are shifted to a usable temperature through compression of process vapor or generated steam.
Plant retrofitting for energy savings
Our heat pump solution made by PILLER is ideally suited for retrofitting existing plants. Its main components can be placed individually. Due to the flexible arrangement - without special requirements regarding the installation site – it is possible to use platforms above the process plants for retrofitting, for example.
Vapor compression or steam generation
Efficient heat recovery systems for your process
There is a simple answer to this question: If vapors from the process can be compressed directly and then be used for heating, the basic principle is Mechanical Vapor Compression. If the waste heat stream is liquid or a vapor that cannot be directly compressed, the heat pump cycle with evaporator (steam generator) is the solution.
In the conventional version of vapor (re-)compression, the PILLER blowers and compressors directly compress the vapor to the temperature/pressure level needed for heat supply. The compressed vapor can be used as a direct heat source for different processes or to be used to generate steam or hot water.
The heat pump cycle with evaporator is the right choice when there are no gaseous waste heat sources or if the vapor can or should not be compressed. The difference: the heat pump system begins with the generation of steam in an evaporator. Water is normally used as refrigerant, so that steam at low pressure and temperature is generated in the evaporator.
Within this system, key components are the PILLER VapoLine products. These units compress the steam in a series of stages to achieve the necessary pressure level, resulting in the production of steam at a usable boiling temperature. The recovered heating steam can then be utilized to supply heat to the same process or to other processes by integrating it into a steam network.
Components & Variations
Customized heat pump systems for multiple applications
As usual, the components are designed according to the specified process data. For the most efficient and economical solution. For your success.
Evaporator for steam generation
The basis for steam generation with the heat pump solution made by PILLER is the evaporator. The evaporator is designed to optimally recover waste, providing the desired steam supply.
How an evaporator works as a steam generator:
The available waste heat, i.e., overhead vapor, is directed to the evaporator. In the evaporator, the overhead vapor is condensed (phase transition), releasing its latent heat.
The Evaporator transfers this heat to the water, evaporating it at low pressure or temperature levels. The major advantage of this form of heat transfer is its ability to operate at very low temperature differences. Water is preferred, as it has a very high evaporation enthalpy.
Almost all the heat can be transferred at a high temperature level. Compared to other refrigerants – such as those frequently used in heat pumps – steam is also environmentally friendly, harmless, inexpensive and can be applied anywhere.
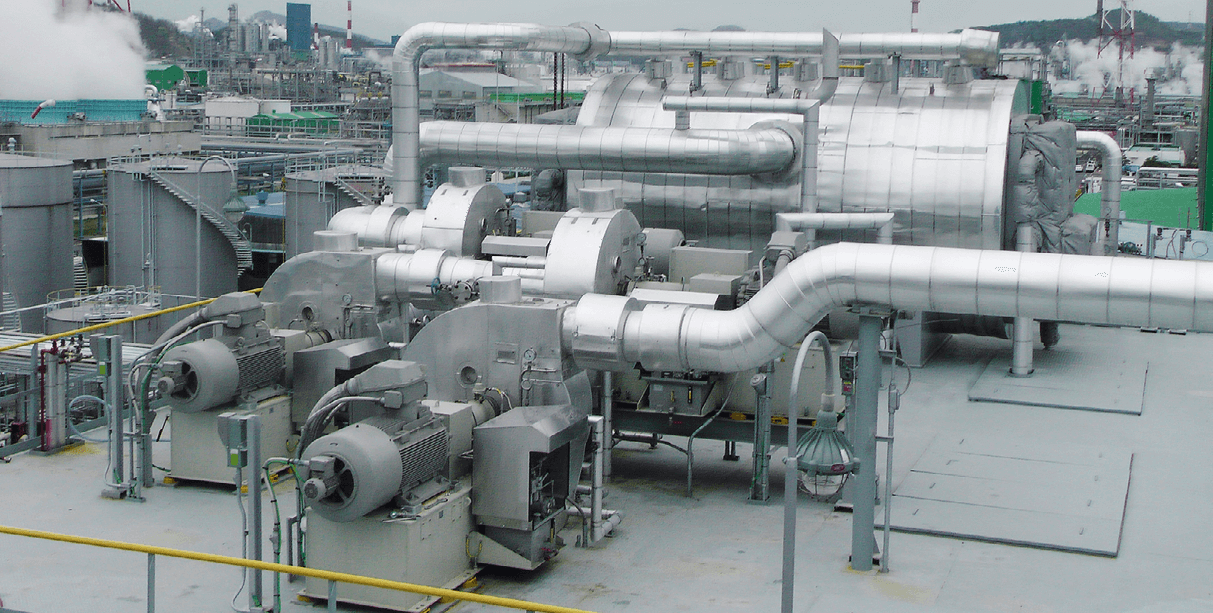
PILLER superior blower and compressor technology
The key element of our heat pump solution made by PILLER is the compression with our superior blower and compressor technology.
The design of the individual blowers and compressors and their interconnection in a serial connect system are perfectly adapted in order to achieve the needed compression of the working fluid. With the retrofitted process, vapor can now be compressed while preserving energy and feeding it at the lowest cost into the processes.
A serial connect system also enables the integration of additional heat sources into intermediate stages. More and more companies are successfully relying on this solution.
By offering the critical components of waste heat recovery processes, we are helping the industry to achieve economic and environmental benefits. PILLER also offers system engineering services, including the conceptual design as well as support in the Pre-FEED phase.
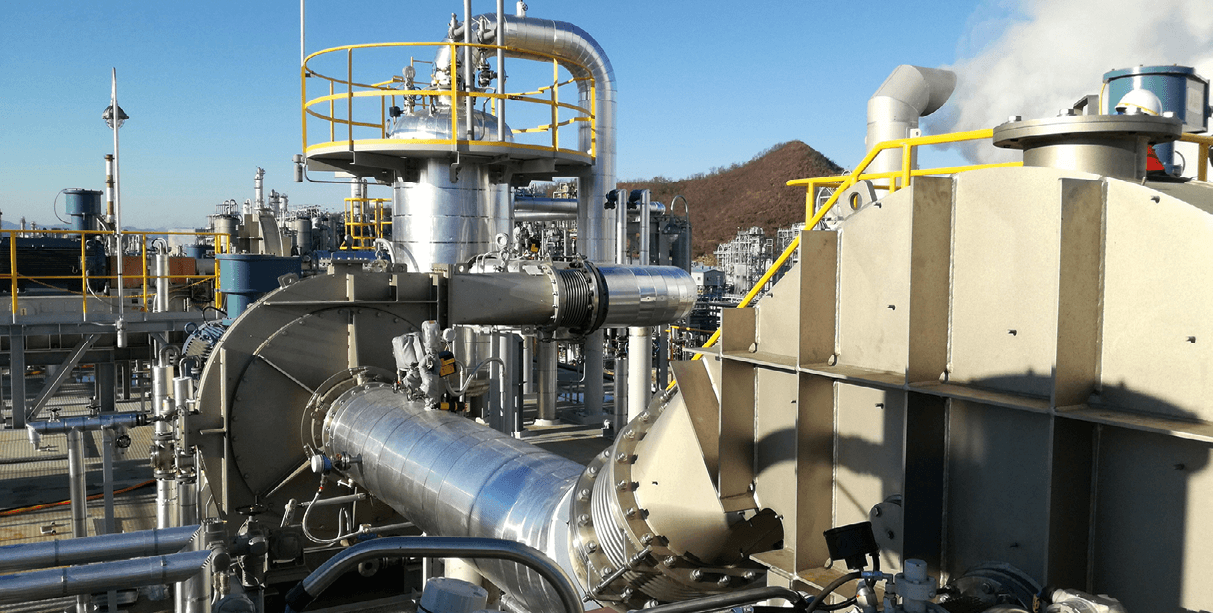
Learn more about PILLER
Contact
Piller Blowers & Compressors GmbH
Nienhagener Str. 6
37186 Moringen
Germany
+49 5554 201-0
+49 5554 201-271