About Chivas Brothers
Chivas Brothers - the Scotch Whisky business of Pernod Ricard
Chivas Brothers is the Scotch whisky business of Pernod Ricard. Chivas Brothers’ award-winning portfolio features some of the world’s most revered Scotch whisky brands including Chivas Regal, Ballantine’s, Royal Salute, Aberlour and The Glenlivet, comprising 13 whisky distilleries, one bottling facility and more than 300 warehouses across Scotland. As both a traditional and a future-oriented company, the Scotch whisky experts work towards the goal of producing "sustainable Scotch" and are therefore taking appropriate steps along their entire value chain.
In line with Pernod Ricard’s 2030 Sustainability and Responsibility roadmap, this includes the elimination of waste and reducing carbon emissions in the growing of natural ingredients, packaging and transportation – as well as transforming the distillation process. In this area, Chivas Brothers has set an industry-leading target of carbon neutrality by 2026.
Distillation at Chivas Brothers
How MVR technology paves the way for reaching carbon neutral distillation at Chivas Brothers by 2026
Chivas Brothers, the Scotch whisky business of Pernod Ricard, is working to achieve carbon neutral distillation by 2026. To reach this industry-leading target, the implementation of enhanced heat recovery technologies is key. For both upgrading existing and equipping new plants, Chivas Brothers relied on PILLER VapoFans, which in a vapor compression heat pump system, delivered a COP of 12 in this project.
Well established, but energy intensive distillation process
Traditionally, the malt whisky is produced in batch distillation using copper pot stills . After the pot still has been filled with the alcohol containing feed, boilers powered by natural gas or other fossil-based fuels provide the steam to the reboilers, that heat the still. „The distillation process usually takes several hours and is very energy-intensive“, says Gregor Schumm, Head of Process Engineering at Piller Blowers & Compressors.
Besides the very high energy costs, heating with fossil fuel-based steam boilers is linked to high CO2 emissions. Unfortunately, most of the energy used to provide the heat for the distillation process in the first place is released into the environment via cooling towers after condensing the alcohol. „After analysing the distillation process in order to reach our goal of carbon neutral distillation by 2026, we came up with the idea to use high-efficiency Mechanical Vapor Recompression (MVR) technology to complement our widely used Thermal Vapour Re-compression technology (TVR)“, says Neil Fraser, Engineering Manager at Chivas Brothers.
„The heat recovery technology allows Chivas Brothers to recover the energy from the product vapor formerly lost via the cooling towers and use it to boil the still, thereby significantly reducing carbon emissions.”
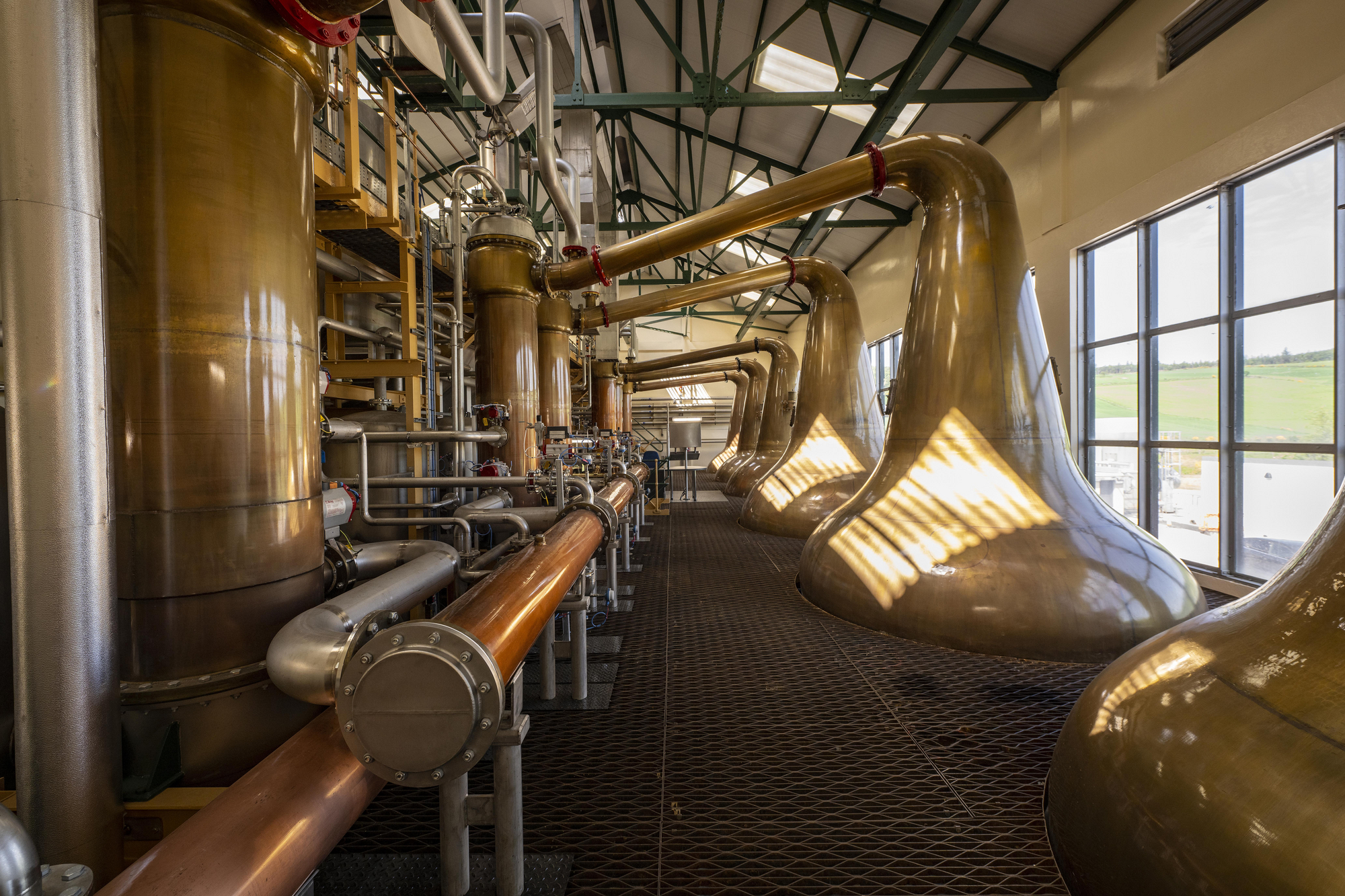


Winning combination: Redesigned process relying on PILLER MVR technology
„Our MVR process is based on two main components that constitute the heap pump system. A vertical condenser and an MVR set consisting of three PILLER VapoFans in series”, explains Chivas Brothers´ Engineer Manager, Neil Fraser. In the new set-up the latent heat of the product vapors leaving the pot still is recovered by the vertical condenser. This heat exchanger produces low-pressure steam (LPS) with a temperature a couple degrees lower than the condensation temperature of the product.
Key to high efficiency is to avoid any subcooling and pressure losses on both sides. Therefore, falling film evaporators are perfect to recover steam from the condensing overheads. The generated low-pressure steam is compressed by a three-stage VapoFan system and subsequently supplied to the still’s reboiler for heating at higher pressure and temperature. „In a single pot, around 1 MW heating duty of the reboiler is supplied by using 90 kW of electric power", Gregor Schumm of PILLER adds. The steam generator is recovering 1500 to 1600 kg/h of vapour at around 80 degrees Celsius. The incorporated water injection saturates the steam feeding to the reboilers and amplifies the efficiency.
Vapor compression heat pump technology

High adaptability for compelling results
What makes the heat pump based on PILLER mechanical vapor recompression technology a perfect fit to Chivas Brothers´ needs are the great flexibility of operation and variable frequency drives of the VapoFans. „The heat pump system adopts to the ever changing process conditions during distillation, providing the compression needed at every stage of the process“, Gregor Schumm points out.
Starting at high temperature difference over the process at the beginning of the batch, the speed is reduced to the end, where more and more water is condensed on the steam generator. The higher water content increases the distillate temperature, resulting a higher satuartion pressure for the vapor compression.
„The continuous adaption to the needs of the process boosts up the efficiency even higher. Starting at a COP of 9, the batch ends with a COP around 20, resulting in an average COP around 12“, says process engineer Oscar Sgrott of PILLER. The COP is defined as the relationship between the thermal power (kW) that is supplied by a heat pump for heating, and the power (kW) that is supplied to the compressor or compressors. As soon as a batch is distilled after a few hours, the VapoFans are simply ramped down in two minutes and ready for the next batch to be distilled.
Hence, compression on demand in combination with high efficiency MVR machines leads to substantial COP numbers. Neil Fraser of Chivas Brothers mentions another big plus for Chivas Brothers: „Water as a heat transfer medium is the ideal way to combine product and environmental safety with high efficiencies by heat pumps directly on the process unit.“
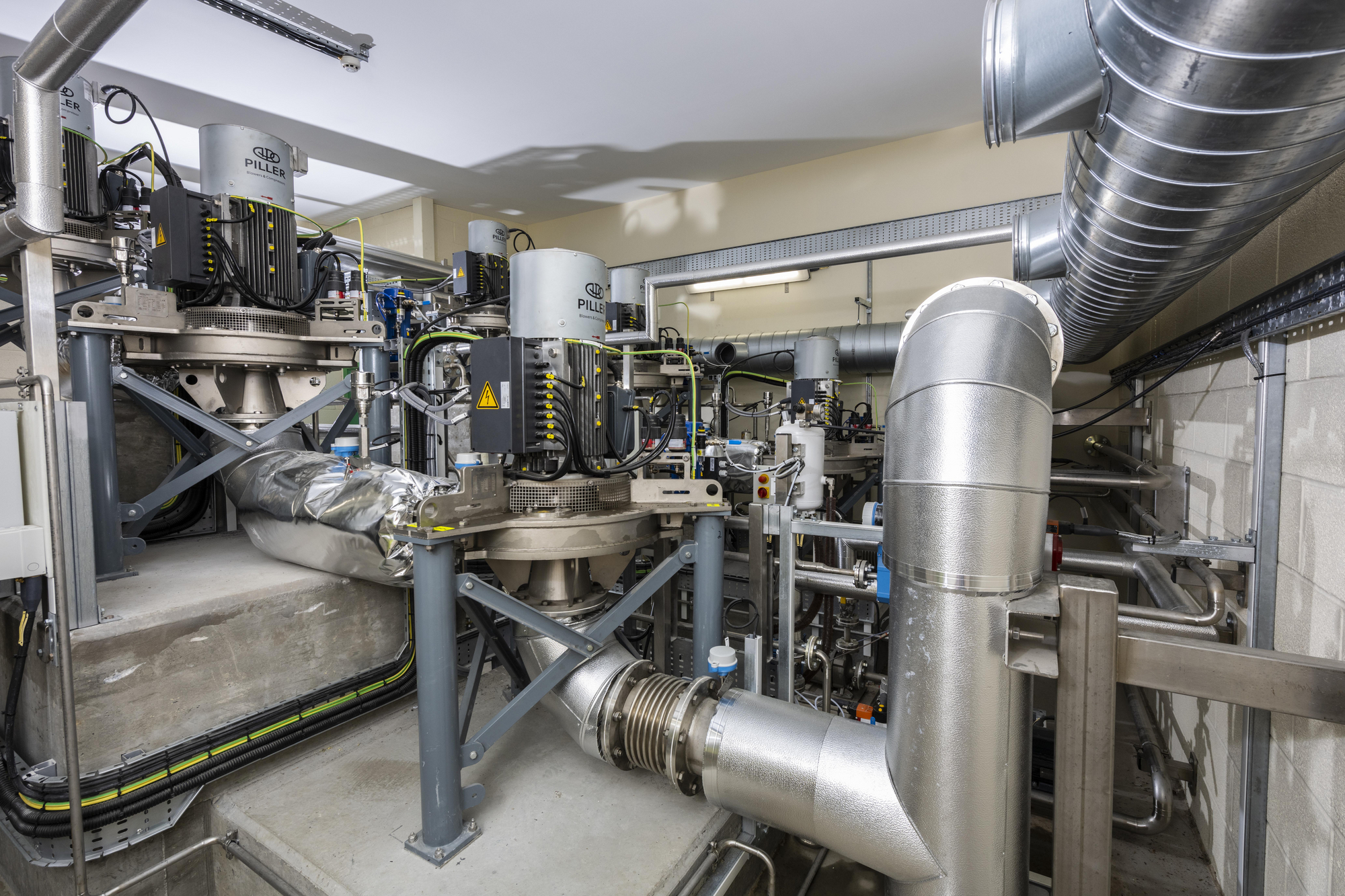

From pilot to company-wide rollout
A successful pilot of the MVR technology was implemented in 2021 at the Glentauchers distillery in Mulben, Scotland. The project, in part funded by the Scottish Industrial Energy Transformation Fund led to an 88% percent energy reduction on a single wash pot still.
Based on the success, Chivas Brothers decided to install two further MVR heat pumps on wash stills at the Glentauchers´ location. Sharing the data from the pilot project with PILLER resulted in the improvement of the MVR design, resulting in an average COP increase from 10 to 12 between phases 1 and 2.
To date, the installations along with TVR on the spirit stills have reduced total energy consumption almost by half (48%) at Chivas Brothers’ Glentauchers distillery site, near Keith in Speyside, Scotland, reducing its total carbon emissions by 53% as a result. The carbon emissions have been reduced from 8,290 tonnes CO2 to 3,970 tonnes CO2 per year on full production.
As MVR technology is considered a major step towards the ambitious target of carbon neutral whisky distillation by 2026 at Chivas Brothers, the company recently announced as part of its FY23 financial results in September an investment of more than £60 million over the next three years towards their ambition for carbon neutral distillation.
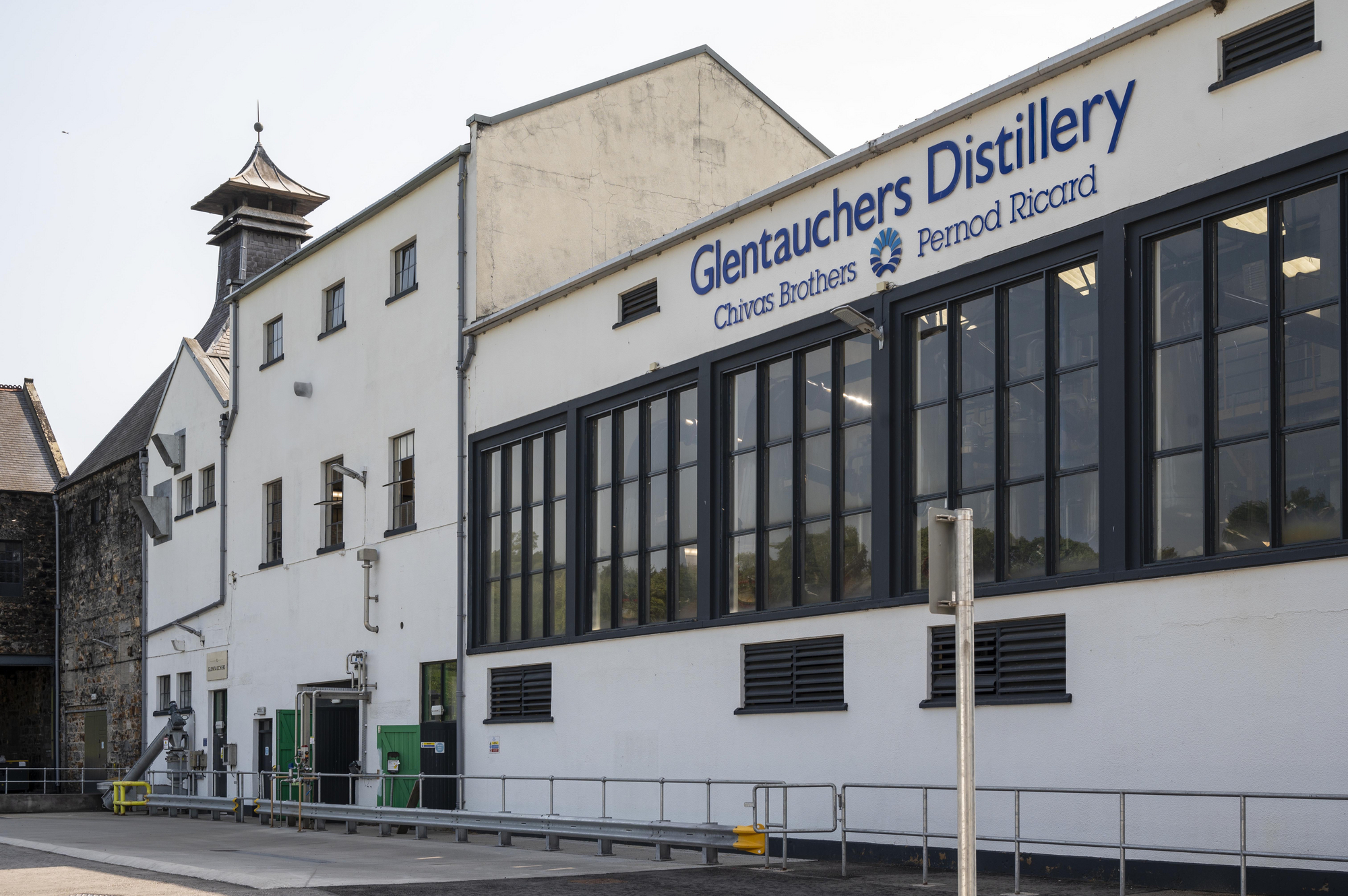
Further information about the Case Study
Would you like to find out more about the project? Here you will find an open source case study and a design study from Chivas Brothers.
Learn more about PILLER
Contact
Piller Blowers & Compressors GmbH
Nienhagener Str. 6
37186 Moringen
Germany
+49 5554 201-0
+49 5554 201-271