Sustainability at PILLER
We all have responsibility for shaping our shared future. As an internationally operating, family-owned company, we see ourselves as a key player whose actions have a significant impact on both the environment and our society.
Actively working towards a livable, greener future by reducing the burden on the environment is an obligation and incentive for us with a view to future generations. For us, the sustainable, responsible use of our planet's finite resources is a task that we must tackle and can no longer postpone.
In addition to this ecological aspect, the social aspect and long-term economic performance are also pillars of sustainability for our responsible corporate actions. For us, sustained economic success is linked to the creation and preservation of sustainable, safe and meaningful jobs - and to respectful collaboration and long-term relationships with our employees, our suppliers, our partners and, last but not least, our customers around the world.
As part of the community, it is natural for us to be socially involved locally at our locations: We regularly support institutions, clubs and initiatives with a focus on offerings for children and young people.
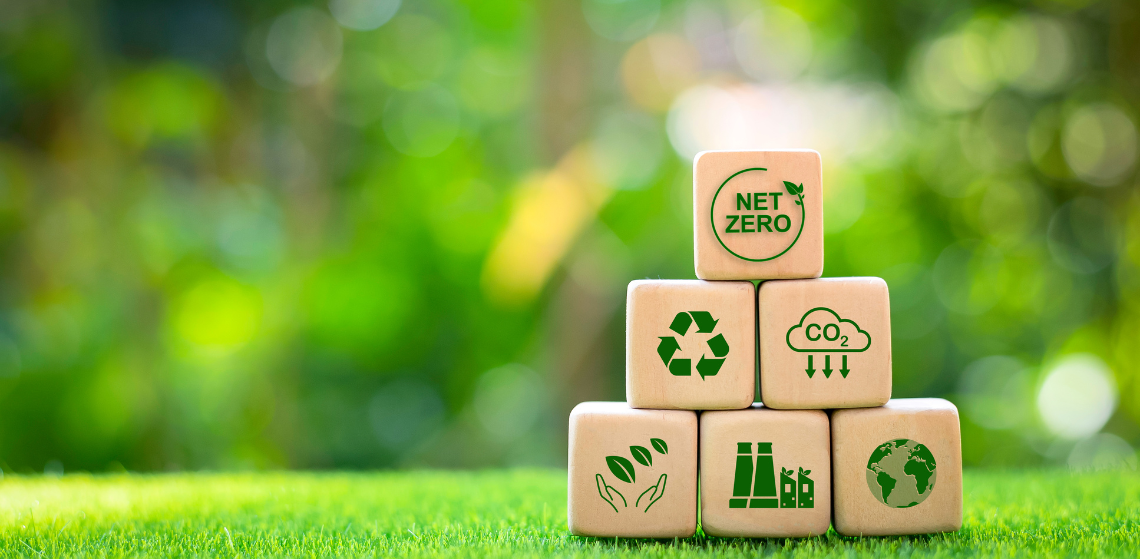
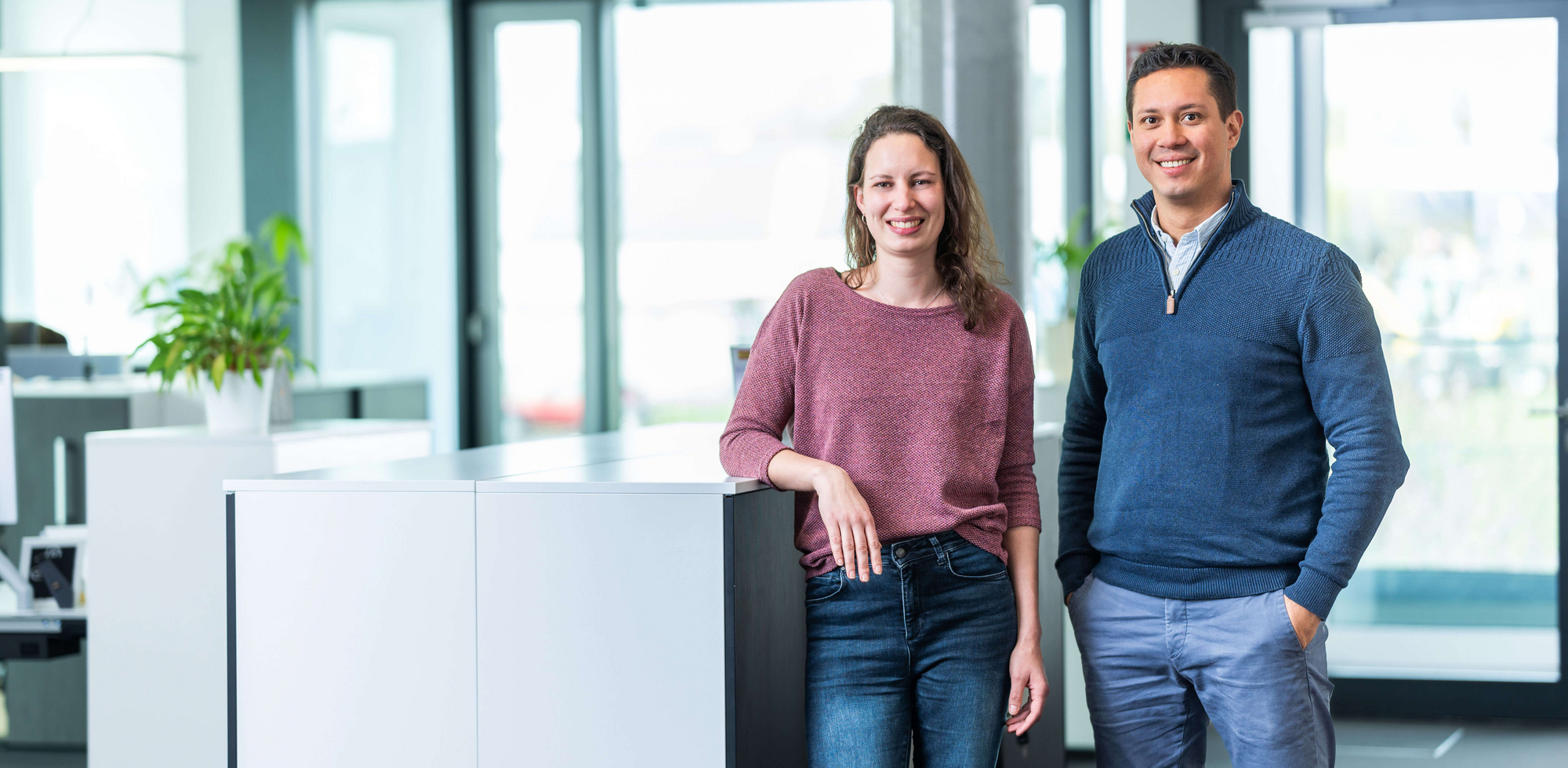
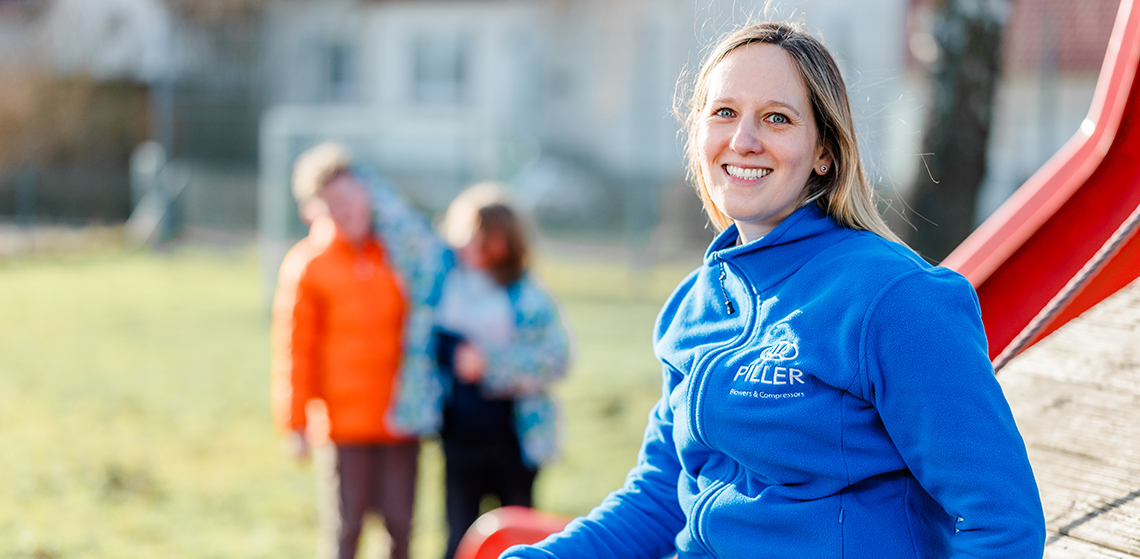
Promote sustainability in production in two ways
Here at PILLER we have two levers to advance sustainable production. With our technology, we help companies in the process industry to significantly reduce their energy use and CO2 emissions. At the same time, we continually put our own processes and products to the test in search of ways to produce more sustainably.
We have developed a unique, innovative technology for heat recovery in industry: Our blowers and compressors specifically for Mechanical Vapor Recompression (MVR) and vapor recovery processes significantly increase energy efficiency in steam processes, reduce the costs of primary energy and lead to CO2 savings in the processes.
Proven are:

reduced energy requirements

reduces CO2 emissions

energy cost savings
What does this actually mean in numbers for customers?
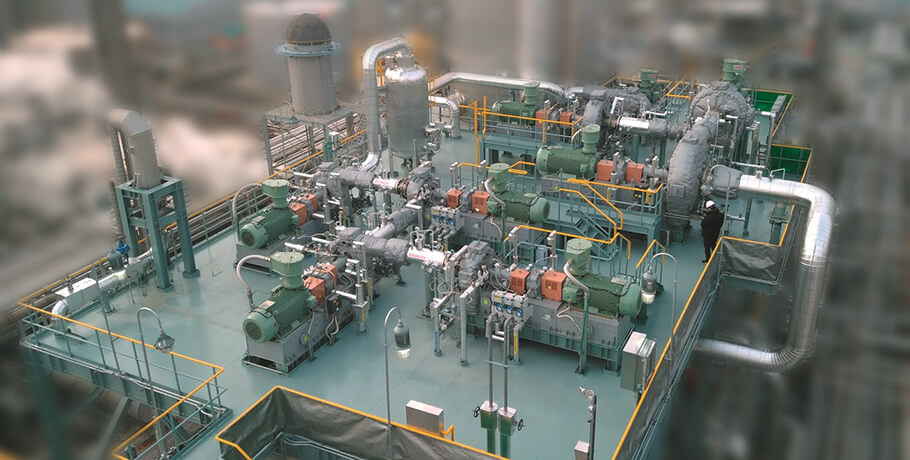
Integration of an industrial heat pump from PILLER into cumene production:
- 42 tons of steam are supplied to other processes per hour
- Energy requirements fall by around 76 percent
- The energy cost savings add up 8 million euros annually
CO2 emissions are reduced by around 58 percent - this corresponds to 10,650 tons per year.
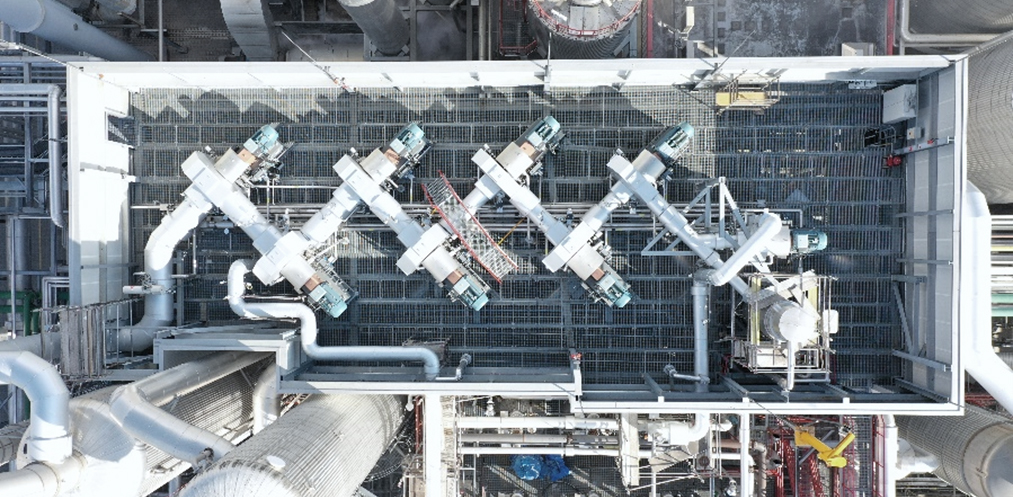
Integration of an industrial heat pump from PILLER in ethanol production:
- A mass flow of 37 tons is moved per hour
- The energy requirement of the system is halved
- Amortization of investment costs in 2 to 3 years
CO2 emissions are reduced by around 50,000 tons per year.
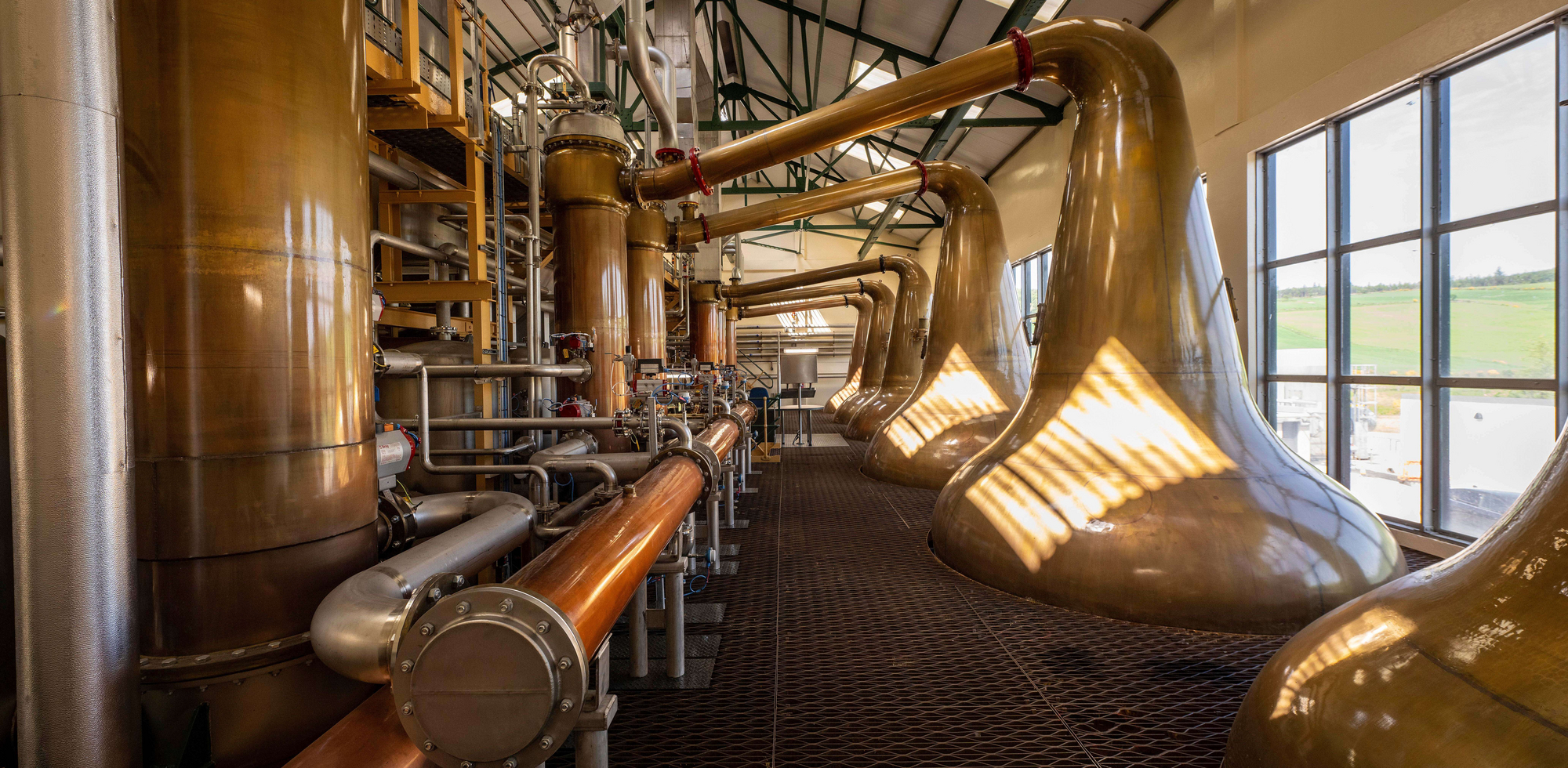
Integration of PILLER machines into the whiskey distillation process at Chivas Brothers:
- Reducing energy consumption by 48 percent
- The energy saved could power 4,979 homes in the UK for a year
CO2 emissions were reduced by 53 percent – the equivalent of 4,320 tons per year.
What do we do here at PILLER?
ALWAYS ADVANCING is not just our claim, but our basic attitude. We want to continually improve our processes, our products and our organization in the spirit of sustainability. That is why we continually put our processes to the test and invest in R&D.
By installing a PV system at our headquarters in Moringen, we have taken a big step towards a smaller CO2 footprint. It also increases independence from external energy suppliers. We use most of the energy we generate ourselves; we only feed a fraction into the grid.
Facts from our PV system
Our investments in R&D also pay off in the area of sustainability: We have developed an additive manufacturing process (3D printing process) for open impellers made of high-strength stainless steel, which has many advantages over conventional milling from solid material. In conventional production, wheels with a diameter of 560 mm and a final weight of 26 kg are milled from 440 kg of solid material.
94 percent of the material ends up as waste. In additive manufacturing this is less than 40 percent. Combined with the lower energy consumption of the manufacturing process, the innovative process reduces the C02 footprint in the production of our machines.
The Initiative Blue Competence
We are a proud partner of the sustainability initiative Blue Competence of the VDMA. The goals of the initiative are to promote sustainability in mechanical and plant engineering, but also to make sustainable solutions known in the industry. We can fully identify with the twelve sustainability principles of mechanical and plant engineering and are committed to adhering to them through our partnership.
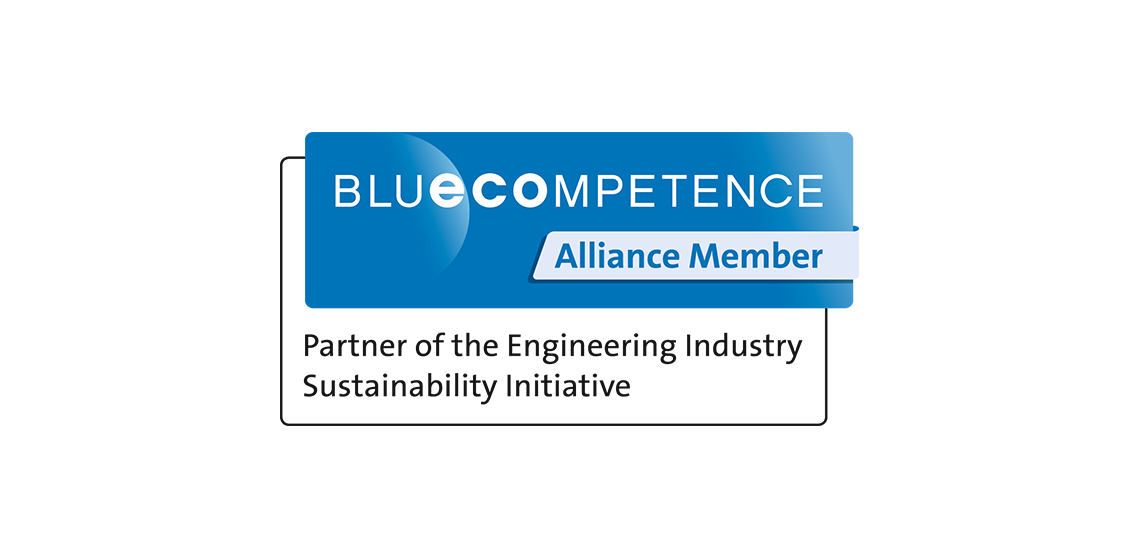
Learn more about PILLER
Contact
Piller Blowers & Compressors GmbH
Nienhagener Str. 6
37186 Moringen
Germany
+49 5554 201-0
+49 5554 201-271